Understanding and Calculating Your Labor Costs: The Ultimate Step-By-Step Guide
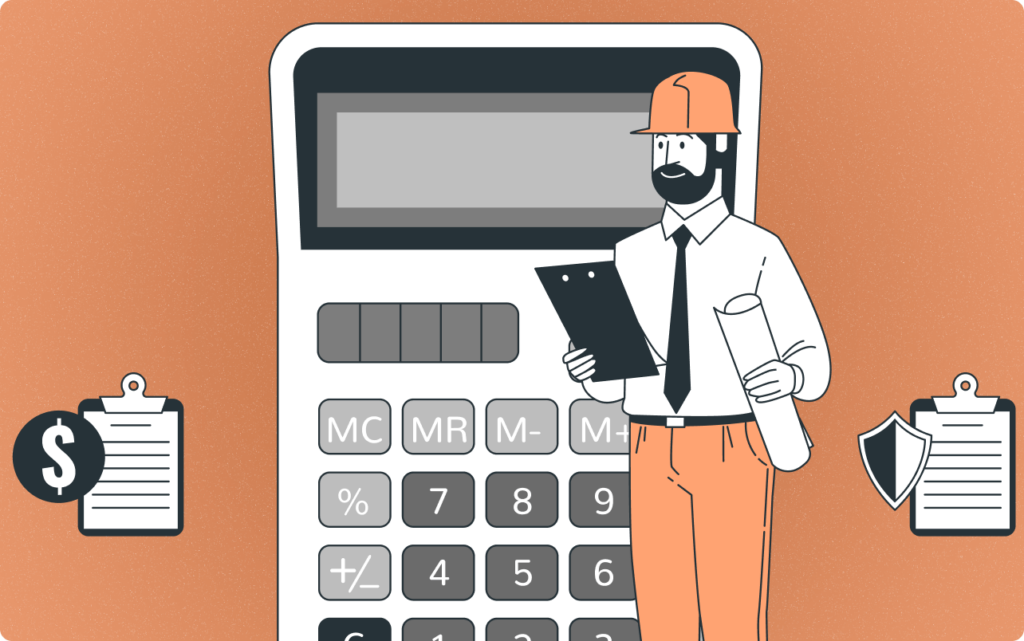
Factors Affecting Labor Costs
Skill Level
The skill level of your workforce is a primary determinant of labor costs. Highly skilled employees typically command higher wages due to the specialized knowledge or expertise they bring to the job. Conversely, positions requiring less specialized skills may have lower associated labor costs. It’s important to balance the need for skilled labor with the cost implications for your business.
Consider the following when evaluating skill level impact on labor costs:
- Complexity of Tasks: More complex tasks require higher skill levels, which can increase labor costs.
- Training and Development: Investing in employee training can enhance skill levels, potentially leading to higher productivity and, in some cases, higher wages.
- Industry Standards: Certain industries have established standards for skill levels, which can influence wage expectations and labor costs.
By understanding the relationship between skill level and labor costs, businesses can make informed decisions about staffing and wage structures.
Market Demand
Market demand plays a pivotal role in determining labor costs. The law of supply and demand dictates that when the demand for a particular skill set is high and the supply is low, the cost of labor for those skills will increase. Conversely, if there is an abundance of workers with a certain skill and a low demand for it, wages are likely to be lower.
Industries experiencing rapid growth or those with seasonal peaks often face higher labor costs due to increased market demand. For example, the tech industry frequently requires specialized skills that are in short supply, leading to higher wages for qualified professionals. In contrast, industries with a surplus of workers may see wage stagnation.
To illustrate how market demand can affect various industries, consider the following table showing the average wage increase percentage over the past year for different sectors:
Industry | Average Wage Increase (%) |
---|---|
Technology | 5.2 |
Healthcare | 4.0 |
Manufacturing | 2.8 |
Retail | 1.5 |
This data highlights the variability of labor costs across sectors and underscores the importance of understanding market trends when calculating labor expenses.
Employee Benefits
Employee benefits are a significant component of labor costs that extend beyond the basic salary or hourly wage. These benefits can include health insurance, retirement plans, paid time off, and other perks that contribute to the overall compensation package. While they are an essential tool for attracting and retaining talent, they also represent a cost that must be carefully managed.
The following table outlines common employee benefits and their potential impact on labor costs:
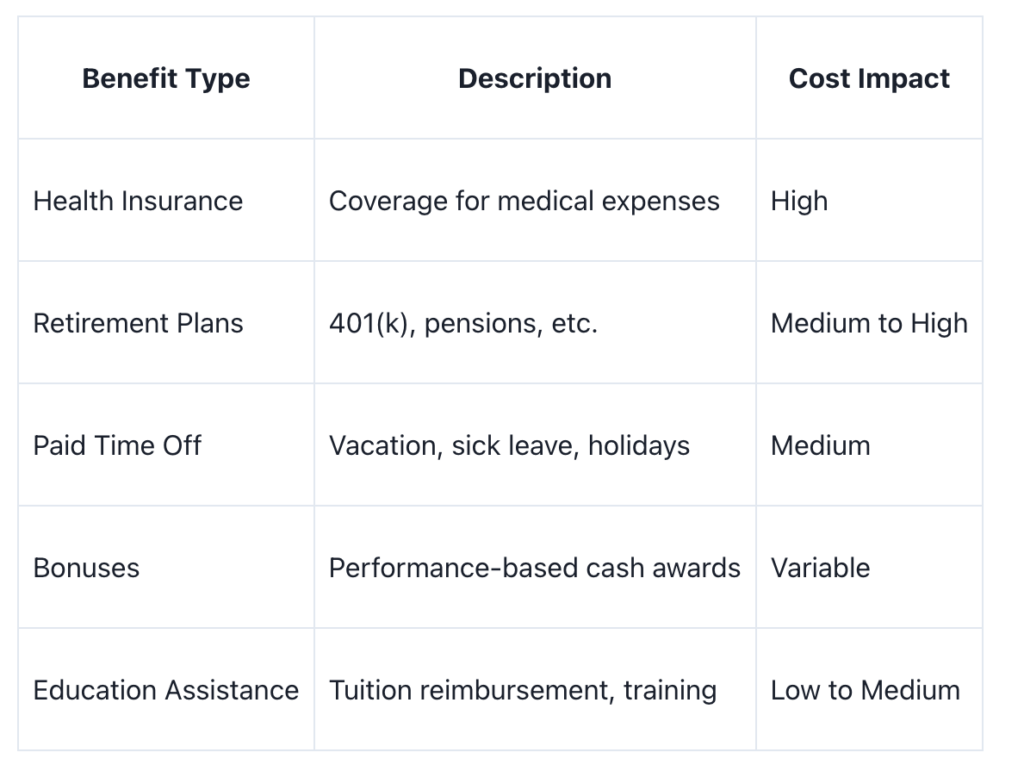
To effectively manage these costs, employers must balance the competitiveness of their benefits package with the financial implications for the business. This requires a strategic approach to benefits design and a clear understanding of how each benefit influences employee satisfaction and the company’s bottom line.
Get more out of your business
Get the best employee engagement content every week via mailing list
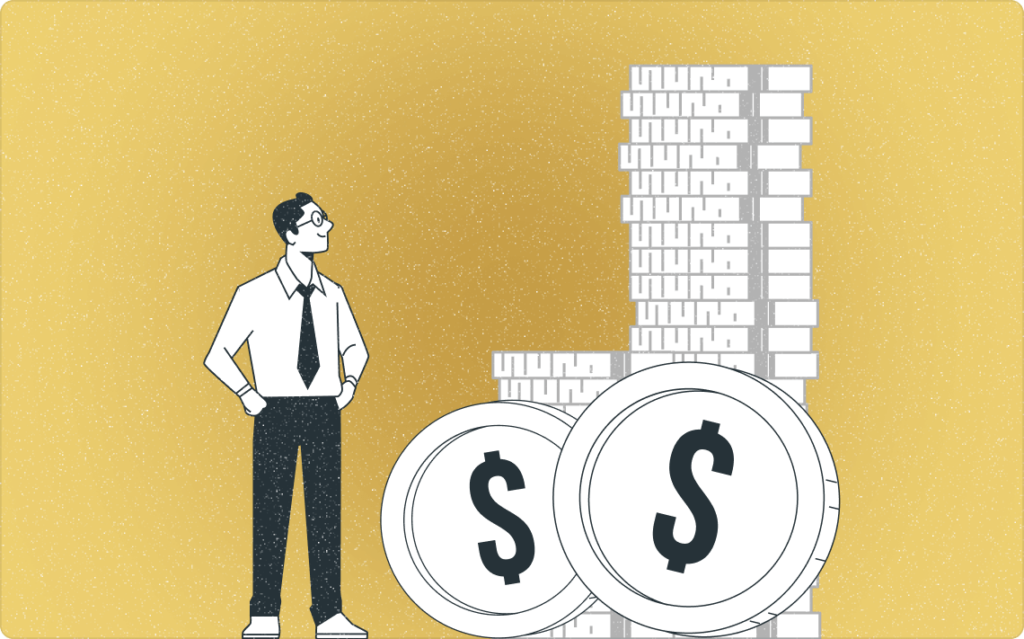
Direct Labor Cost Online Calculator
[labor_cost_calculator]
Calculating Direct Labor Costs
Hourly Wage
The hourly wage is the foundational element when calculating direct labor costs. It is the amount paid for each hour of work performed by an employee. To accurately assess labor costs, businesses must first determine the standard hourly rate for each position, which can vary based on experience, skill level, and job responsibilities.
To illustrate, consider the following table showing different hourly wages for various positions within a company:
Position | Hourly Wage |
---|---|
Entry-Level | $15.00 |
Mid-Level | $25.00 |
Senior-Level | $35.00 |
Specialist | $45.00 |
Once the hourly wage is established, it’s multiplied by the number of hours worked to calculate the total direct labor cost for a given period. This calculation forms the basis for budgeting and financial planning, as well as pricing strategies for products and services.
Overtime Costs
Understanding overtime costs is crucial for accurately calculating your labor expenses. Overtime is typically paid when employees work beyond their standard hours, and the rate is often higher than the regular pay. In the United States, for example, the Fair Labor Standards Act (FLSA) requires that overtime pay is at least one and a half times the employee’s regular hourly rate for hours worked over 40 in a workweek.
To effectively manage overtime costs, it’s important to track the number of overtime hours worked and the associated pay rates. Below is a simplified example of how overtime costs might be calculated for a single employee in a given week:
Day of the Week | Regular Hours | Overtime Hours | Regular Rate | Overtime Rate | Total Earnings |
---|---|---|---|---|---|
Monday | 8 | 0 | $20 | – | $160 |
Tuesday | 8 | 0 | $20 | – | $160 |
Wednesday | 8 | 2 | $20 | $30 | $220 |
Thursday | 8 | 2 | $20 | $30 | $220 |
Friday | 8 | 0 | $20 | – | $160 |
Saturday | – | – | – | – | – |
Sunday | – | – | – | – | – |
Total | 40 | 4 | – | – | $960 |
It’s also important to consider the impact of overtime on employee well-being and productivity. Consistently relying on overtime can lead to burnout and decreased efficiency. Therefore, it’s essential to balance the need for overtime with the health and satisfaction of your workforce.
Productivity Rates
Understanding productivity rates is crucial when calculating labor costs, as they directly impact the efficiency and cost-effectiveness of your workforce. Productivity rates can be measured by the output per employee within a given time frame. This metric helps businesses to determine the actual cost of labor per unit of output, which is essential for pricing and profitability analysis.
To effectively measure productivity rates, consider the following steps:
By regularly monitoring and seeking to improve productivity rates, businesses can optimize their labor costs and enhance their competitive edge. It’s also important to recognize that productivity is influenced by factors such as employee morale, workplace environment, and the use of technology, which should be considered in any analysis.
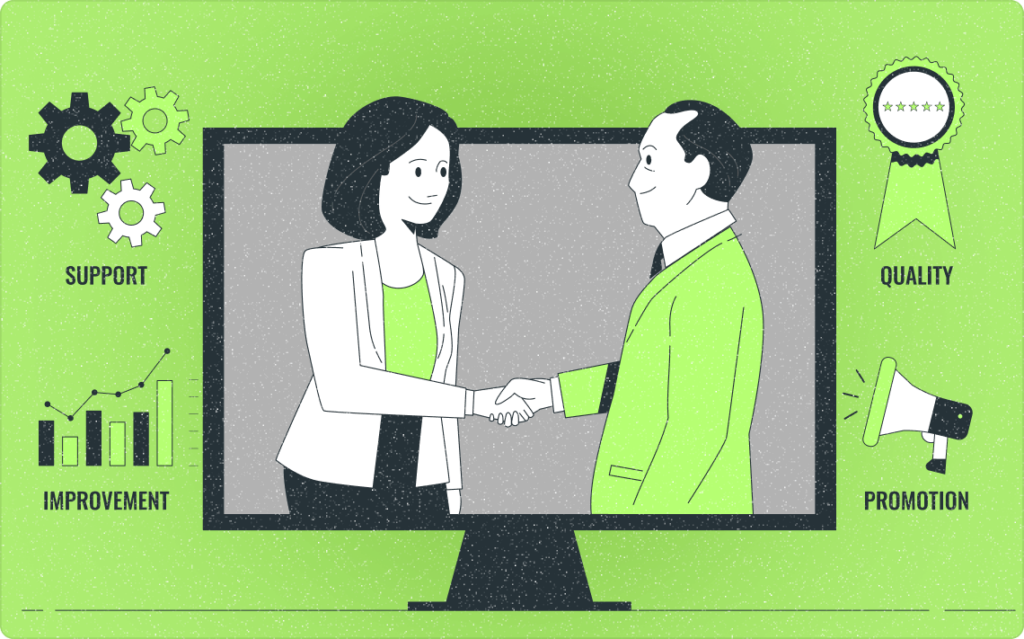
Indirect Labor Costs
Training Expenses
Investing in employee training is a critical component of indirect labor costs. Effective training programs can lead to increased productivity and reduced errors, but they also require a significant upfront investment. The costs associated with training can vary widely depending on the complexity of the job and the methods used for training.
Here’s a breakdown of potential training-related expenses:
- Training Materials: Manuals, online courses, and interactive software.
- Instructor Fees: Costs for hiring external trainers or compensating internal staff.
- Facility Costs: Renting space for training sessions if in-house facilities are not available.
- Equipment: Purchasing or renting specialized equipment for training purposes.
- Employee Time: Wages paid to employees while they are being trained, not contributing directly to production.
It’s important to track these expenses accurately to understand their impact on overall labor costs. Some companies use a cost-benefit analysis to determine the return on investment for training expenditures, ensuring that the long-term benefits justify the initial costs.
Administrative Costs
Administrative costs are often overlooked when calculating labor costs, yet they play a crucial role in the overall financial health of a business. These costs encompass the expenses related to the general administration and management of a company. They include salaries of administrative personnel, office supplies, and equipment, as well as costs associated with information systems and technology support.
To manage these costs effectively, it’s important to track them meticulously. Below is an example of how administrative costs might be categorized and tracked on a monthly basis:
Category | Description | Monthly Cost |
---|---|---|
Salaries | Salaries for administrative staff | $X,XXX |
Office Supplies | Paper, ink and other supplies | $XXX |
Technology | Software licenses and IT support | $X,XXX |
By regularly reviewing this table, businesses can identify areas where they might reduce expenses or improve efficiency. For instance, bulk purchasing of office supplies or negotiating better rates for technology services can lead to significant savings over time.
Employee Turnover
Employee turnover can significantly impact indirect labor costs. It encompasses the expenses associated with replacing employees who leave your company. These costs are not always obvious but can accumulate quickly, affecting your bottom line.
When an employee departs, the company incurs costs in several areas:
- Recruitment: Advertising, interviewing, and screening potential candidates require both time and money.
- Training: New employees need to be brought up to speed, which involves training resources and the time of experienced staff.
- Lost Productivity: It takes time for new hires to reach the productivity levels of their predecessors.
- Cultural Impact: High turnover can affect team morale and the overall workplace culture.
To manage and reduce employee turnover costs, consider the following strategies:
By addressing these areas, businesses can mitigate the financial strain of high turnover and maintain a more stable and productive workforce.
Conclusion
In this comprehensive guide, we have explored the intricacies of understanding and calculating labor costs. From defining labor costs to breaking down the step-by-step process of calculating them, we have provided valuable insights for businesses and individuals alike. By mastering the art of labor cost calculation, you can make informed decisions, optimize your resources, and enhance your financial management. Remember, labor costs play a crucial role in the success and sustainability of any venture. With the knowledge gained from this guide, you are now equipped to navigate the complexities of labor cost analysis with confidence and precision.
Frequently Asked Questions
How do skill levels affect labor costs?
Skill levels can impact labor costs by influencing the wages paid to employees. Higher skilled workers often command higher wages, which can increase labor costs.
What is market demand in relation to labor costs?
Market demand refers to the level of demand for labor in the market. Higher market demand can lead to increased wages and labor costs for businesses.
What are employee benefits and how do they impact labor costs?
Employee benefits are additional perks or compensations provided to employees, such as health insurance or paid time off. Offering benefits can increase labor costs for employers.
How are direct labor costs calculated?
Direct labor costs are calculated by multiplying the hourly wage of employees by the number of hours worked, including overtime costs, and factoring in productivity rates.
What are indirect labor costs and how do they differ from direct labor costs?
Indirect labor costs are expenses related to labor that are not directly tied to specific employees or projects, such as training expenses, administrative costs, and costs associated with employee turnover.